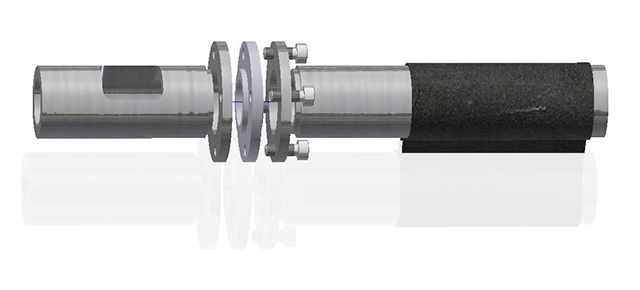
Dziś chciałbym przedstawić kolejną porcję opisu prac nad moją wytłaczarką, zauważyłem parę problemów z którymi systematycznie daje sobie radę, niestety ostatnio brak czasu dał się we znaki, ale już nadrabiam
Po paru próbach nieudanego wytłaczania filamentu doszedłem do wniosku, że trzeba zmienić geometrię ślimaka. Programem firmy Campuplast obliczyłem potrzebne parametry takie jak głębokość kanałów, długości stref, kąt pochylenia linii śrubowej i inne dostosowane do wydajności wytłaczania. Dla przypomnienia, ślimak wytłaczarki składa się zazwyczaj z trzech odcinków:
Strefa zasilania służy do pobrania materiału z leja zasypowego, podgrzanie i zagęszczenie mieszanki a następnie transport do kolejnej strefy.
W strefie sprężania zachodzi dalsze zagęszczanie mieszanki. W tej strefie materiał przechodzi ze stanu stałego w uplastyczniony.
W strefie dozowania powinno następować ujednorodnienie mechaniczne i termiczne przetwarzanego materiału, oraz podwyższenie temperatury do takiej wartości aby możliwe było pokonanie oporów przepływu przez głowicę.
Na podstawie wyliczonych parametrów ślimak skrócono, a kanały zostały pogłębione, dzięki czemu napęd ślimaka będzie miał mniej oporów do pokonania, a wymiary całego urządzenia się zmniejszą.
Zmiany dotyczyły też dzielonego cylindra. Dzielony cylinder zastosowano, aby wyeliminować konieczność chłodzenia strefy zasilania. Pomiędzy dwoma częściami cylindra znajduje się pierścień z PTFE ( potocznie zwanym teflonem/tarflenem). Teflon jednak nie jest tworzywem konstrukcyjnym i przy temperaturze sięgającej 200 stopni w podwyższonym ciśnieniu zaczyna płynąć, co objawiało się zniszczeniem pierścienia i wypłynięciem masy przetwarzanego tworzywa poza cylinder, co widać na poniższym zdjęciu.
Dobrym pomysłem było przesunięcie łączenia cylindrów w kierunku napędu. Materiał przetwarzany, nie jest jeszcze w tym miejscu do końca uplastyczniony, a grzałka oddaliła się od feralnej teflonowej części. Co ciekawe, teflon po pewnym czasie zaczął się rozpadać i kruszyć, a jego kawałki zaczęły pojawiać się w wytłaczanym profilu.
Wykonano też analizę termiczną złożonego cylindra:
Jak widać, pierścień z teflonu zapewnia odpowiednią izolację dwóch części cylindra, przy temperaturze grzałki równej 190 ˚C, w części zasypowej uzyskano temperaturę wynoszącą ok. 96 ˚C . Temperatura ta pozwala na to, aby granulki znajdujące się w zasobniku nie zostały uplastycznione przed podaniem ich do odpowiedniej strefy przez ślimak.
Następna część już niebawem, postaram się przybliżyć efekty i zaburzenia przepływu w głowicy, a także skupić się na połączeniu głowicy i kalibratora, co będzie miało kluczowe znaczenie dla średnicy i wyglądu wytłaczanego profilu – filamentu.