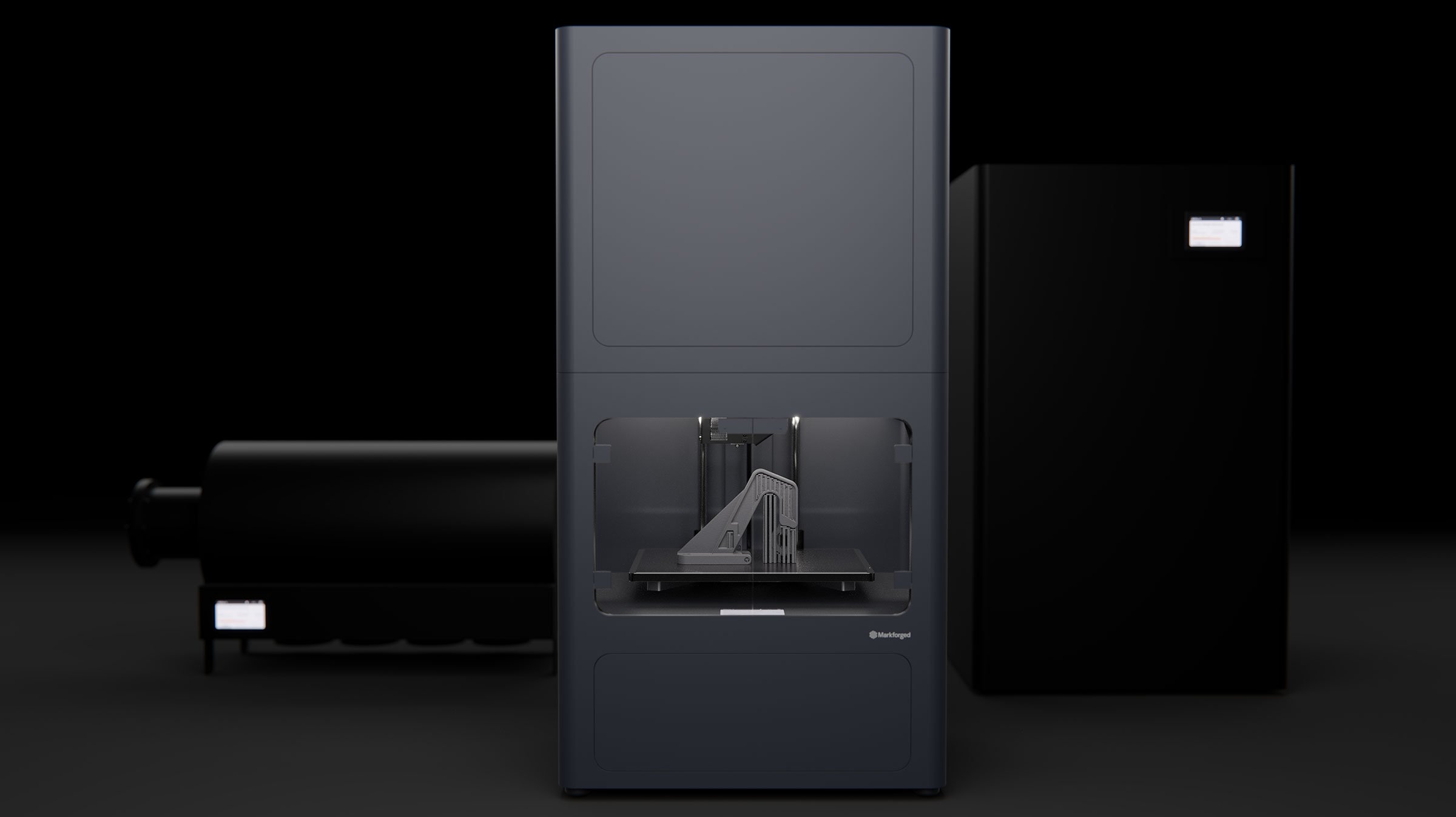
Metoda druku 3D do tworzenia części metalowych, opiera się na wytłaczaniu materiału (FDM/FFF), który jest mieszanką metalu i środków wiążących na bazie polimeru.
Nazwa technologii „Atomic Diffusion Additive Manufacturing” jest opatentowana przez firmę Markforged.
Proszki metali są zamknięte w polimerze, aby uzyskać stałą postać materiału, dzięki czemu można je wytłaczać podobnie jak w metodzie FDM/FFF. Wytworzona w ten sposób część przechodzi jednoetapowy proces termiczny (spiekania) w piecu o specjalnie dobranym profilu temperatury w zależności od użytego materiału.
ADAM wytwarza części o gęstości 99,7%. Części są tak mocne jak części odlewane lub kute. Drukowane w ten sposób elementy wykazują izotropowe właściwości mechaniczne (mierzone w każdej osi właściwości mechaniczne są porównywalne). Niektóre materiały, takie jak np. stal narzędziowa H13 nadaje się do procesu odpuszczania, czyli podniesienia właściwości mechanicznych, szczególnie zwiększenie udarności materiału.
Proces ADAM umożliwia budowanie w pełni zamkniętych struktur siatkowych, w wyniku czego powstają części o wysokim stosunku wytrzymałości do masy. Systemy proszkowe mają tę wadę, że zatrzymują niespieczony materiał w zamkniętych strukturach, co utrudnia lub uniemożliwia jego usunięcie, w tym przypadku to zjawisko nie występuje.
Proces druku 3D
Proces tworzenia części podzielony jest na szereg etapów:
- Tworzenie designu i cięcie na warstwy – w tej części zaprojektowaną część importuje się do programu Eiger i wybiera materiał z jakiego ma być wydrukowany element. Program automatycznie tnie wybrany element na warstwy i dodaje podpory tam, gdzie są niezbędne
- Druk 3D – drukowany jest kształt części z proszku metalu w powłoce plastikowej. Części są skalowane w górę, aby skompensować skurcz podczas procesu spiekania
- Mycie – po wydrukowaniu, części trafiają do urządzenia myjącego Wash-1, gdzie odbywa się rozpuszczanie większości plastikowego materiału wiążącego
- Spiekanie – umyte części umieszczane są w specjalnym piecu, gdzie są poddane wygrzewaniu przy odpowiednio dobranym profilu temperaturowym w zależności od materiału. Pozostałe spoiwo zostaje wypalone, a proszek metalowy zestalony
Materiały
Materiały stosowane w technologii ADAM:
- 17-4 PH Stainless Steel – łączy wysoką wytrzymałość, odporność na korozję i twardość. Używany w wielu różnych zastosowaniach produkcyjnych
- H13 Tool Steel – stal narzędziowa do pracy w wysokich temperaturach, doskonała odporność na zużycie
- A2 Tool Steel – może być hartowany powietrzem do 58 HRC, doskonała odporność na uderzenia. Służy do tworzenia oprzyrządowania, stempli i matryc
- D2 Tool Steel – może być hartowany powietrzem do 60 HRC, wysoka odporność na ścieranie. Idealny do narzędzi i wykrojników
- Inconel 625 – stop niklu, który świetnie znajduje zastosowanie w wysokich temperaturach i środowiskach korozyjnych. Stosowany w przemyśle motoryzacyjnym i lotniczym
- Miedź – wysoka przewodność cieplna i elektryczna. Idealny do druku radiatorów, niestandardowych elementów przewodzących i innych złożonych geometrycznie części
- 316L Stainless Steel – doskonała odporność na korozję. Używany w zastosowaniach morskich. Dalej rozwijany
- Titanium Ti6Al4V – Doskonały stosunek wytrzymałości do masy. Biokompatybilny. Stosowany w lotnictwie, medycynie a także jubilerstwie
Urządzenia
Drukarki wykorzystujące tą technologię:
- Metal X System firmy Markforged
Metal X dysponuje przestrzenią roboczą o wymiarach: 300 mm x 220 mm x 180 mm. Całkowita wielkość urządzenia do druku to 575 mm x 467 mm x 1120 mm. Dodatkowo urządzenie posiada kamerę do zdalnego monitorowania procesu drukowania. Metal X posiada enkodery, które w czasie rzeczywistym kontrolują, czy drukarka wykonała prawidłowo zadaną zmianę pozycji głowicy.
Drukarka Metal X sama nie myje części ani ich nie spieka, dlatego Markforged oferuje również średniej wielkości piec SINTER-1 i jego większego brata SINTER-2 do dużych wydruków, oraz stację do mycia części o nazwie WASH-1. Wszystkie te urządzenia są niezbędne, aby prawidłowo wykonać element w technologii ADAM.
Oprogramowanie
Eiger to autorski program do cięcia modeli na warstwy i przygotowywania części bezpośrednio do wydruku. Jest dostępny w trzech konfiguracjach: przeglądarkowej, aplikacji komputerowej z pamięcią lokalną i całkowicie offline. Wersja przeglądarkowa, która działa w chmurze dostępna jest tylko i wyłącznie przez przeglądarkę Google Chrome.
Po wyborze materiału i pieca, który będzie użyty do wypiekania części, program uwzględnia skurcz materiału podczas tego procesu i odpowiednio go skaluje, tak aby po całym procesie część była zgodna wymiarowo z danym projektem.
Eiger umożliwia zarządzanie siecią drukarek i wydruków Markforged w jednym miejscu. Nadzoruje aktywność i wydajność drukowania, niezależnie od tego, czy jest to jedna czy dwadzieścia drukarek połączone w tzw. „farmę drukarek”.
„Slicer” Markforged obsługuje również druk z tworzyw wzmacnianych włóknami węglowymi.
Program po cięciu, generuje pliki MFP (MarkForged Print), które zawierają plik gcode i są widzialne przez drukarki MarkForged.
Koszty
Koszt samego urządzenia drukującego Metal X to ok 400 tys zł, dodatkowo trzeba zaopatrzyć się w myjkę Wash-1 za ok 41 tys zł i piec do wypiekania wydrukowanego elementu – mniejszy SINTER-1 ok 250 tys zł lub większy piec SINTER-2, dający możliwość spiekania elementu o maksymalnym polu roboczym drukarki Metal X, a to za ok 500 tys zł (Dane na: maj 2020)
Koszt całego systemu do druku metodą ADAM nie jest już niski i w zależności jak duże elementy chcemy produkować, będą kosztować z mniejszym piecem ok 700 tys zł, z większym o przestrzeni takiej jak pole robocze drukarki – ok 950 tys zł (Dane na: maj 2020)
Od firmy Markforged dostaliśmy wydruk testowy w technologii ADAM, jest to otwieracz do butelek wykonany z materiału 17-4 PH Stainless Steel. Element wygląda jak wydruk FDM/FFF z niewyregulowanym dobrze przepływem filamentu w wysokości warstwy ok. 0.2 mm. Nie wpływa to negatywnie na funkcjonalność części, ale pierwsze wrażenie jak na wydruk, którym producent chce przekonać do siebie potencjalnego klienta jest mało reklamowy. Po otrzymanym modelu ciężko powiedzieć coś na temat jego tolerancji wymiarowej, ponieważ nie mamy projektu do którego moglibyśmy się odnieść. Producent podaje, że czas wydruku tego modelu to 54 min, natomiast do tego czasu musimy doliczyć mycie i wypalanie elementu, co może go parokrotnie wydłużyć.
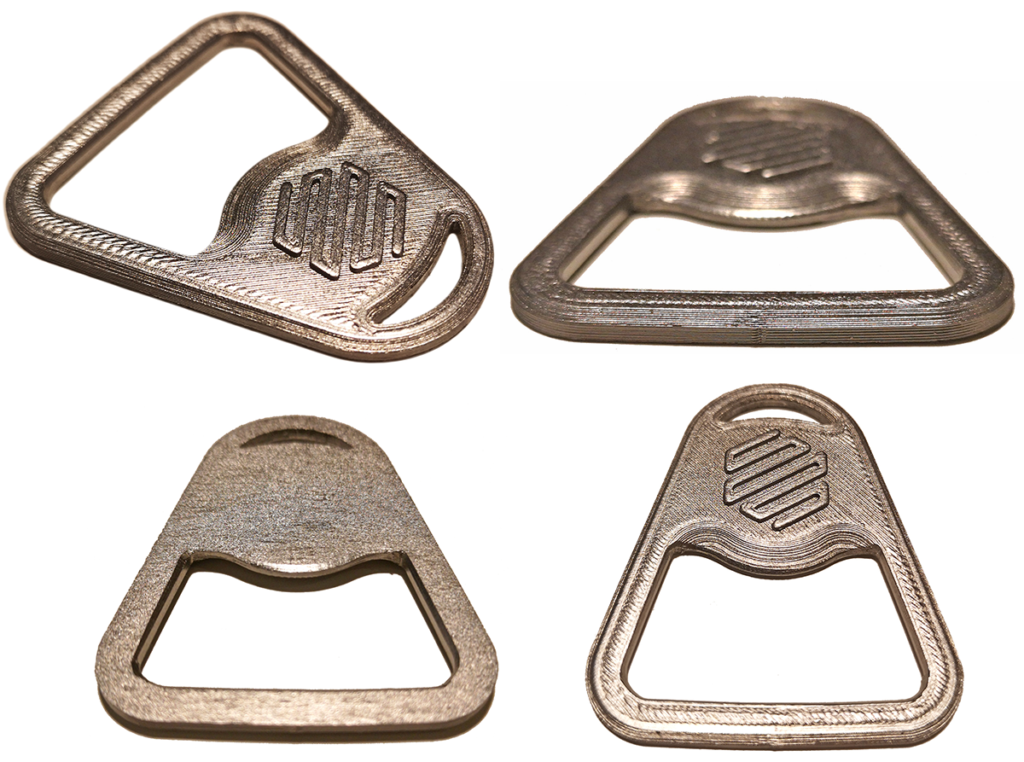
Reasumując, części wykonane w technologii ADAM mogą być ciekawą alternatywną do droższych systemów proszkowych DMLS.
Źródło: markforged.com